Feuilles de caoutchouc naturel are flat materials derived from natural rubber (mainly polyisoprene), processed using specific techniques. Known for their high elasticity, wear resistance, and compressive strength, natural rubber sheets are widely utilized across various industries, including construction, automotive, and manufacturing. The material’s softness, flexibility, and heat resistance make it ideal for diverse applications.
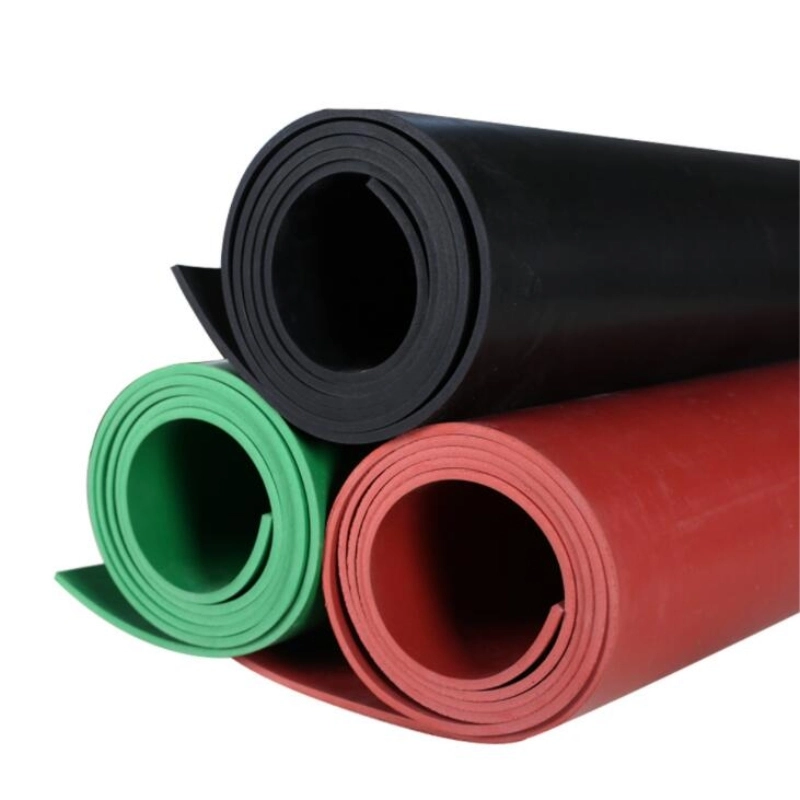
Key Characteristics of Natural Rubber Sheets
- High Elasticity and Flexibility: Natural rubber sheets are renowned for their exceptional elasticity and flexibility. They return to their original shape quickly after being stretched or compressed, making them ideal for shock absorption and vibration damping applications.
- Wear Resistance and Aging Resistance: Due to its natural structure, natural rubber offers superior wear resistance and aging resistance against UV rays and oxidation, outperforming many synthetic rubbers in longevity.
- Résistance chimique: Natural rubber demonstrates excellent resistance to chemicals, particularly oils, acids, and alkalis. This makes it highly suitable for industrial environments that involve exposure to such substances.
- Cold-Weather Performance: Even in low temperatures, natural rubber retains its elasticity and flexibility, making it an ideal material for outdoor equipment, cold storage, and other cold environment applications.
Natural Rubber vs. Synthetic Rubber
Natural rubber and synthetic rubber may seem similar but differ significantly in their raw materials, performance, and applications:
- Raw Material Source: Natural rubber is extracted from the latex of rubber trees (Hevea brasiliensis), primarily found in tropical climates. Synthetic rubber, in contrast, is produced through chemical processes using petroleum-based products.
- Performance: While natural rubber excels in elasticity, wear resistance, and aging resistance, synthetic rubber offers better performance in areas like oil resistance, chemical stability, and ozone resistance.
- Production and Cost: Natural rubber production is influenced by climate and geography, making it subject to variability. Synthetic rubber, on the other hand, is mass-produced in controlled environments and generally costs less to manufacture.
Where Does Natural Rubber Come From?
The primary source of natural rubber is the rubber tree (Hevea brasiliensis), which thrives in tropical regions, such as Southeast Asia, Africa, and South America. Latex, the milky sap from the rubber tree, is the raw material for natural rubber. The tapping process involves cutting the tree’s bark to collect latex, which is then processed through several steps: preservation, concentration, and vulcanization.
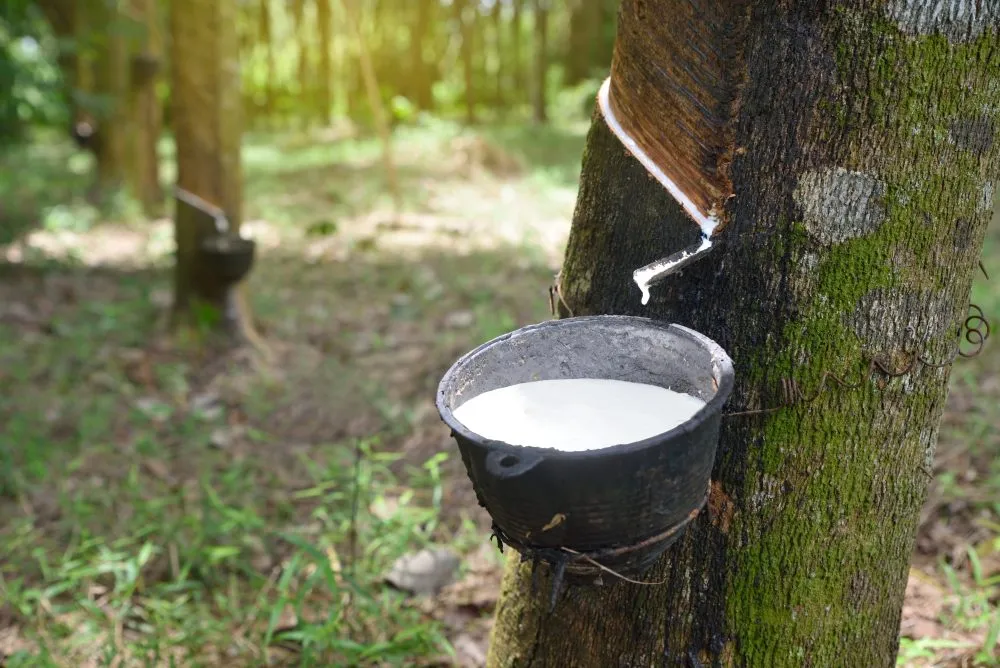
Common Processing Methods for Natural Rubber Sheets
- Cold Processing: This technique is used for temperature-sensitive applications, ensuring minimal impact on the rubber’s properties. It is ideal for products requiring low thermal exposure.
- Hot Vulcanization: Vulcanization involves mixing natural rubber with sulfur and heating it to form cross-linked bonds, resulting in a more durable and heat-resistant product. It is the most common method used for manufacturing high-performance natural rubber sheets.
- Calendering: This involves heating natural rubber and pressing it into thin sheets. It is frequently used for creating rubber films, gaskets, and rubber tapes.
Applications of Natural Rubber Sheets
Natural rubber rolls are highly versatile and can be used in a wide range of industries:
- Automotive: For manufacturing gaskets, seals, and vibration dampers.
- Construction: As insulation, flooring, and shock-absorbing mats.
- Manufacturing: In industrial belts, protective covers, and machinery components.
Conclusion
Natural rubber sheets stand out for their superior elasticity, wear resistance, and aging resistance, making them a popular choice in various industrial applications. Although synthetic rubber may be more cost-effective for certain uses, natural rubber still holds an edge in performance for products requiring exceptional elasticity and resilience. The rubber tree remains the primary source of natural rubber, and advanced processing methods like vulcanization and calendering ensure the production of high-quality sheets for diverse uses.
By understanding the fundamental properties and manufacturing processes of feuilles de caoutchouc naturel, industries can select the most suitable material for their specific needs, ensuring the best performance in their applications.